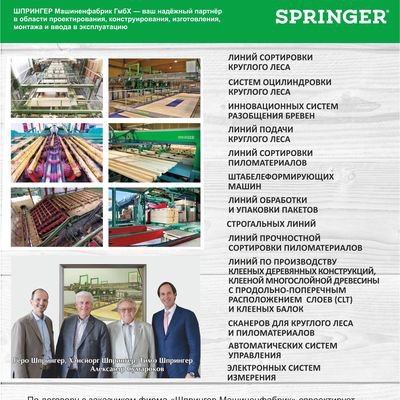
Вирус подталкивает к автоматизации!
20 апреля 2020
В начале
карантина по коронавирусу работали только предприятия с непрерывным циклом
производства. В ЛПК непрерывное производство только ЦБП, все остальные
производства на время карантина приостановили свою деятельность. Никто не даст
гарантии, что после завершения борьбы с СОVID-19 не появится ещё более опасный
вирус, о чём предупреждают виднейшие вирусологи мира. А значит, лесопильщики и
деревообработчики должны быть готовы к очередной пандемии. И появилась тема для
обсуждения: как повлияет коварный вирус на деятельность лесопереработчиков
России и всего мира? С традиционным российским вопросом «Что делать?» редакция
обратилась к видному эксперту в области лесопиления и деревообработки,
консультанту австрийской компании «Шпрингер Машиненфабрик» Александру
Сумарокову.
По мнению Александра Михайловича, печальный опыт 2020 года подталкивает лесопромышленников к внесению изменений в технологию лесопереработки, чтобы в условиях любой пандемии не останавливать производство, что, естественно, приведёт к значительным экономическим потерям, а действовать и быть готовыми к любым ситуациям.
В первую очередь потребуется до минимума сократить численность работающих на производстве, руководствуясь необходимостью, чтобы оставшиеся работники при выполнении своих обязанностей не пересекались друг с другом. Можно исключить участие человека в производственном процессе, но ещё не созданы технологии, способные полностью без участия человека управлять производственными процессами лесопереработки.
Чтобы осваивать наши лесные богатства меньшим количеством тружеников, нужно не противиться наступлению так называемой 4-й технической революции, предусматривающей строительство заводов-автоматов. Мир никогда не вернётся к тому состоянию, в котором был накануне пандемии. В развитых странах, в том числе и в России, наблюдается сокращение народонаселения, это неизбежно. Выход один – нужно научиться работать малым числом людей, а именно за счёт высококвалифицированных специалистов, работающих на современном производстве, способном вырабатывать больше продукции. Высококвалифицированный сотрудник становится большой ценностью.
Однако есть ещё одна проблема. Как быть с занятостью работоспособного населения, поскольку любая модернизация ведёт к сокращению рабочих мест. Этого не надо опасаться, поскольку вокруг любого крупного предприятия создаётся целая сеть предприятий малого бизнеса, которые оказывают различные услуги крупному бизнесу, вот здесь и создаются новые рабочие места.
Ещё совсем недавно модернизация производства проводилась исключительно для увеличения прибыли. Сокращение количества людей на производстве не только позволяло снизить расходы на содержание персонала, а в первую очередь влияло на снижение производственного травматизма. А уже сейчас масштабная автоматизация – это первый шаг к созданию лесоперерабатывающих предприятий, способных бесперебойно работать в условиях самых жёстких карантинов. Как ни странно звучит – именно коронавирус показал, как беззащитно лесоперерабатывающее производство перед эпидемией, подтолкнул к полной автоматизации производственных процессов и показал дальновидность бизнесменов и высокопоставленных чиновников, которые уже сейчас принимают меры к кардинальной модернизации производства.
Первым проектом завода-автомата в России по решению региональных властей заинтересовалась Республика Тыва. Особенностью этого проекта является то, что на территории нынешней Республики Тыва практически нет не только высокомеханизированных, автоматизированных предприятий, очень мало предприятий, работающих в лесопереработке.
В основу этого проекта заложено то, что в настоящий момент в Республике Тыва есть богатый запас древесины, только хвойного сырья около 2 млрд. кбм. В основном преобладает тонкомерная лиственница. Это связано с климатическими особенностями региона.
Сейчас пришло время говорить о необходимости создания такого предприятия, и вот почему: есть лес, это лиственница, в транспортной доступности находятся привлекательные рынки сбыта лесопродукции, такие как Япония, Южная Корея, Китай. Теперь Министерством путей сообщения РФ и правительством республики принято решение в течение трёх-четырёх лет построить железную дорогу, небольшой участок длиной около 400 км, от столицы Республики Тыва Кызыла до населённого пункта Куракино.
Главная проблема региона – отсутствие высококвалифицированных кадров. И строительство именно завода-автомата – это острая необходимость. Выход только один – привлекать специалистов из других регионов для работы вахтовым методом. Постепенно прямо на заводе будет производиться обучение специалистов для завода из местных жителей, что позволит перейти от вахтового метода к работе с местным персоналом.
За базу проекта разработчики проекта взяли схему существующих полуавтоматизированных и полностью автоматизированных предприятий Западной Европы, Швеции, Германии и Австрии, которые в данный момент работают. Планируемый объём распиловки до 500 тыс. кбм пиловочника.
Склад сырья представляет собой автоматизированный склад из штабелированного сырья, всё сырьё окорённое и раскладывается сразу в кассеты. На окорке планируется применить самое современное окорочное оборудование.
Все брёвна рассортировываются по диаметрам с градациейдо полсантиметра и укладываются в кассеты. Известно, чем тщательней рассортировано сырьё, тем выше выход пиломатериалов. На складе сырья будет занято 1-2 человека. Из кассет, которые располагаются вдоль сортировки брёвен, сырьё автоматически будет подаваться грейферами, управляемыми в автоматическом режиме и по заданной программе.
Линия «Шпрингер» подаёт пиловочник на конвейер, который подаёт его на линию «Линк», со скоростью распиловки до 100-120 м/мин. Подобная схема уже работает на Лесозаводе 25 в Архангельске.
Линия «Линк» работает в автоматическом режиме, здесь человек только наблюдает за процессом распиловки. При такой скорости подачи брёвен человек даже не способен что-то заметить и изменить в процессе распиловки.
Таким образом, на участке подготовки сырья к распиловке и на распиловке работают 2-4 человека.
Далее – сортировка пиломатериалов. Все выработанные пиломатериалы поступают на линию сортировки сырых пиломатериалов компании «Шпрингер».
Что касается линии штабелирования пиломатериалов, она тоже работает в автоматизированном режиме, формируется стандартный сушильный штабель. Сформированные сушильные штабеля автоматически подаются в сушильные камеры, в процессе загрузки участвует один человек.
В процессе сушки все камеры открываются и закрываются в автоматическом режиме по команде, и далее идёт разборка и сортировка сухих пиломатериалов. Далее высушенные пиломатериалы поступают на линию сортировки сухих пиломатериалов компании «Шпрингер». Здесь в автоматическом режиме полностью оценивается качество пиломатериалов – от качества распиловки до качества самой древесины, включая все пороки древесины.
Вся система сортировки пиломатериалов производится только по одному показателю – прочностному. Потому что основное применение пиломатериалов – изготовление клеёных деревянных конструкций, которые идут на строительство ферм, мостов и т. д., поэтому прочностной показатель главный.
На упаковке пиломатериалов планируется использовать оборудование фирмы «Шпрингер», которое автоматически не только формирует, сжимает, но и упаковывает пакеты пиломатериалов. Здесь работает один человек.
Пакеты автоматически поступают на склад готовой продукции, и каждый пакет пронумеровывается, в базу вносятся все качественные и объёмные показатели пиломатериалов пакета.
Отгрузка пиломатериалов также полностью автоматизирована. Трудится здесь не более трёх человек.
Таким образом, в производственном процессе завода-автомата будет задействовано в одну смену около 20 человек производственного персонала! Все производственные участки завода сбалансированы по объёму переработки, что позволяет максимально эффективно использовать производственное оборудование, исключает дисбаланс производственных мощностей».
Следует добавить, что древесина будет использоваться полностью, планируется производство пеллет, клеёных конструкций, панелей для домостроения CLT, древесные отходы пойдут на отопление. Заготовка леса – сортиментная – харвестерами и форвардерами. Срок окупаемости проекта 5 лет.
Именно такие современные производственные комплексы станут гарантий работы ЛПК России в любых условиях, при любых карантинах.
Беседовал
Сергей КОНДРАТЬЕВ.
Опубликовано в "Лесной Регион" №07(263)
Другие новости по теме: